Compare with other countries which has advantage in labor cost, China has a relatively more mature and more stable electronics manufacturing capabilities and supply chain, it is always the right decision to cooperate with a Chinese manufacturer after R&D stage of your project.
Although you can easily search for many electronic manufacturers from China, due to the different sizes and business models of each company, if you do not choose a matching company based on the actual situation of your project, price and terms misunderstandings and conflicts may arise due to differences in conditions between the two parties.
If this is your first time trying to work with a Chinese electronics manufacturer, we hope these few guidelines can help you choose the right supplier and understand how to maintain a long-term and stable cooperation with it.
Step 1 - Clarify the content of your project production, select 3-5 potential manufacturers and understand their capabilities.
Before you contact a Chinese electronics manufacturer, you can list all your customization demands and see what help you expect from the Chinese manufacturer.
Basically electronics manufacturing included below content:
Mainboard Manufacturing
PCB(Printed Circuit Board) Fabrication
Electronics Component Bom list Sourcing
PCB assembly (PCBA) SMT&THT Assembly
PCBA functional Test
PCBA Aging Test
Coating&Potting Services
Machanical Assembly
Cable&Wire Assembly customization
Enclosures customization and Assembly
Metal Hardware customization
Finish product assembly
Functional testing
Product Aging test
Packing
Since not every Chinese electornics factories is able to offering above services in one roof, some factories are just produce consumer PCB not industrial grade PCB, some just focus on SMT or THT Assembly but not good in Bom cost and procurement, some are not able to offering coating service or functional testing, you may need to shift your products to other factories for other demands to complete your production and need extra time and expense to verify their capabilities and build trust with their people.
Zero Mistake Solutions is established to offer the full series of services in electronics manufacturing for our customers, especially for those clients who just step inside the prototyping stage and production stage. We can offer detailed guidance and help here with our rich experience and reliable local resources.
Step 2 - Get a formal quotation with your manufacturing files and talk to their project manager and understand how rich their project experience is.
A competitive quotation can show whether the company has a supply chain with sufficient advantages to meet your project budget and help you save costs. The price of the bill of materials is often not from one supplier but from many reliable suppliers with guaranteed quality. However, if the cost difference of components of a supplier is greater than that of other suppliers, be careful about the authenticity of the chip.
The quotation time can show whether the company is familiar with the content of your project requirements and also reflect the busyness of the company's projects. Usually, the reasonable quotation time for PCBA is 1-3 days. If the quotation time for a project exceeds 1 week, your inquiry may have been forgotten or their procurement is busy with the ongoing project, then the project delivery date will most likely be delayed.
Usually, the salesperson who communicates with you will be the project manager who is responsible for the progress of the project and solving problems throughout the process. For the process and quality control issues that you are not very clear about, you can consult them and learn about their cooperation attitude and project management experience from their responses. In many Chinese companies, sales people who can use English often do not have an electronic engineering background, but are majoring in English or international trade. When they first enter the electronics manufacturing industry, there is still a lot they need to understand and learn. If you can meet an experienced project manager who has worked for many years, you will have very good production experience, which is even more important than finding a large-scale factory.
Ms. Isabella from Zero Mistake Solutions is a well experienced project manager and been working in electronics field since 2016. She is able to offer constructive solutions and is good at problem solving for our clients. Welcome to talk to her if you have any questions about electronics.
Step 3 - Choose a manufacturer that meets the quality management system of the corresponding industry according to your project category
The common international quality management systems in electornics manufacturing are ISO9001, ISO13485, IATF16949, AS9100.
ISO9001 The basic and widely applied in any manufacturer organization, aiming to improve customer satisfaction and meet the client's demand. A factory certified with ISO9001 system will be able to meet the quality of most products in consumer and industrial field.
ISO13485 The medical device quality management system puts forward special requirements for the quality of medical device manufacturers to ensure the safety and effectiveness of medical devices. If your electronic devices are for medical purposes, please make sure your manufacturer is certified with ISO13485.
IATF16949 The automotive industry quality management system focuses on defect prevention and waste reduction, and improves quality management in the automotive industry supply chain and assembly process. If your products are related to automotive electronics, especially related to safety of automotive systems, please make sure your products will be produced in a factory certified by IATF16949.
AS9100 Aerospace Quality Management System, which specifies quality management requirements for the aviation, space and defense industries, including safety requirements. If your devices are about Aerospace, you could choose a factory certified with AS9100.
But of course, the more certificated they have, means their quality management procedures are more complicated and a lower the acceptance of defetive products. Thus, their manufacturing price is higher. So, it is not the more certification they are getting is better for your project, you should understand which quality management system are suitable for your project.
Zero Mistake Solution is able to choose the suitable factory partner according to your project applications and quality requirements.
Step 4 - Arrange factory tours and check their production facilities. You will know what is real behind the screen.
Some Chinese companies would like to improve the company impression by telling clients they are factory and using factory pictures showing on their website, while they actually a middle company. For example, some of the company is working with a few different scale factory, they will only take their clients to visit the decent one and not the one which really produce their project. When something wrong is happening, they need a thousands lies to explaine the first lie.
Actually, to telling the trueth to our client is never a problem as long as we can solve problems for our clients, becuase working in the manufacturing industry, Zero Mistake Solutions are providing the same even better and comprehansiv services than a factory can offer.
Whenever our client wants to have a tour in a local factory, Zero Mistake Solutions will only lead our clients to the factory and production plant which really produces their project, we will 100% true to our clients.
Step 5 - Check their Solderpaste and storage method
Solderpaste is the only raw material of SMT production. Its quality is very important for the soldering process and the lifetime of the finished board.
The quality of solder paste is mainly related to two factors:
Solder paste brand
Storage method of solder paste
Well-known solder paste brands usually have higher silver content, stronger technological innovation, more environmental protection requirements, and higher reliability in electronic production. The solder paste brands we often use are Senju solder paste from Japan and Alpha solder paste from the United States.
The storage method of solder paste is different from other production tools and materials. It must be stored in the refrigerator throughout the process. The temperature must be strictly controlled and it must be completely sealed to avoid moisture. When taking out the solder paste from the refrigerator, the first-in-first-out principle must be followed. When using it, it needs to go through steps such as warming up and sufficient stirring to ensure that the quality of the solder paste meets the production requirements before use.
Step 6 - Check their Quality Control process
The quality inspection process is an important factor in determining whether a factory can guarantee quality. From incoming material inspection to process inspection, and then to shipment inspection, every step of the production process is carried out.
The following is a relatively standard PCBA quality inspection process that we proceed with Zero Mistake Solutions for your reference:
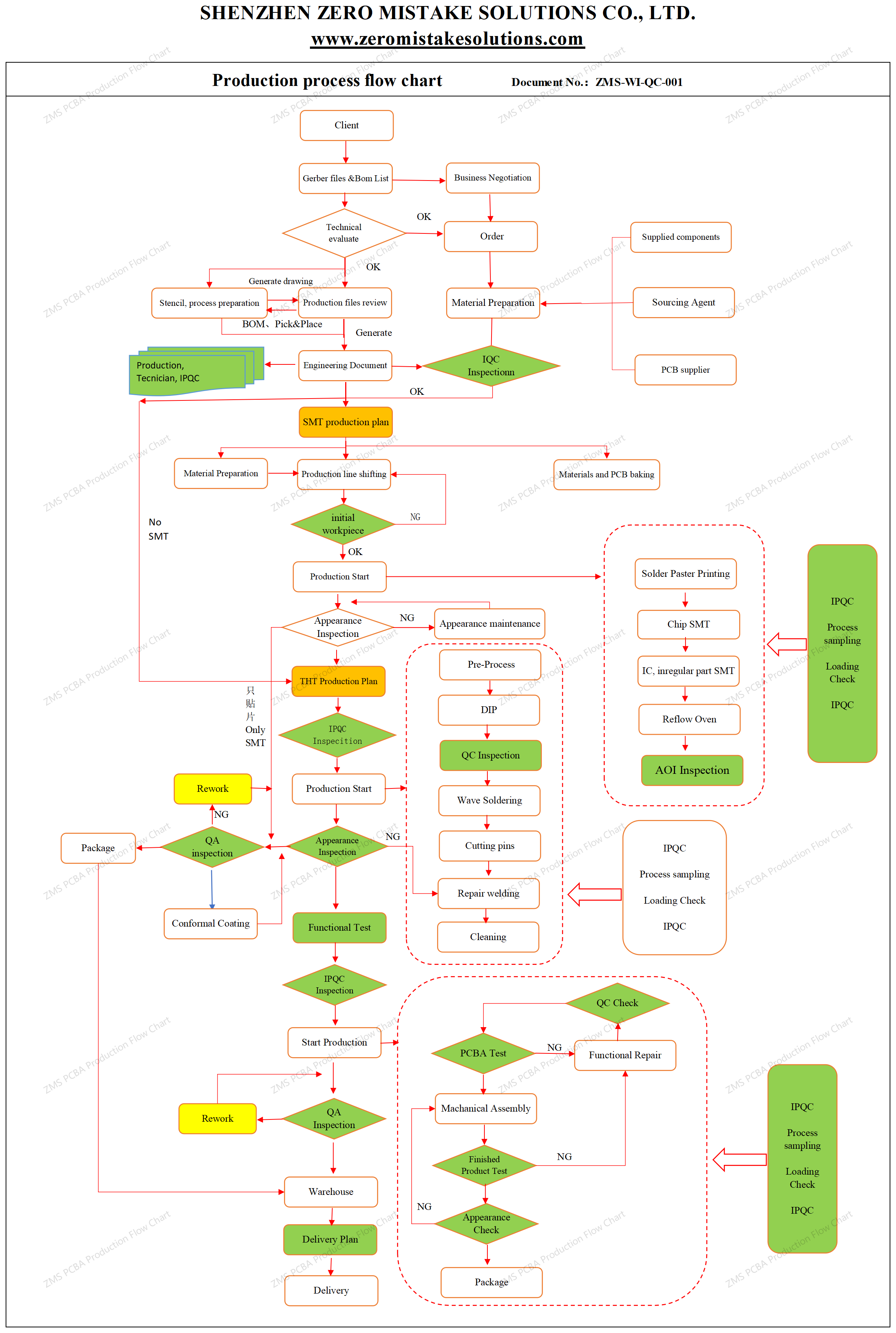
Step 7 - Check if the project manager is able to handling all technical issues and translate well between you and their engineer.
Step 8 - Check their packaging
Because PCBA is very fragile, if the packaging method is not appropriate, it is easy to cause damage such as collision during transportation. If it is not properly packed in anti-static bags, the sensitive components on the circuit board are easily broken down by the static electricity on the human body during transportation. Therefore, Zero Mistake Solutions has been providing customers with anti-static bag packaging and internal anti-vibration and anti-loosening packaging methods.
Step 9 - Check their solutions after you find some defect in their production.
When you receive the manufactured circuit board and are excited to turn it on, you find that it doesn't work. At this time, you will be very disappointed and contact the supplier to inform them of the result.
When you receive the finished circuit board and are excited to start it, you find that it does not work. You will be very disappointed and contact the supplier to inform them of the result.
At this time, please do not conclude that it is the supplier's fault. The following is the correct way to solve the problem:
If you are an engineer yourself, you can use a multimeter to analyze the circuit of the product first, check whether the voltage on the line does not meet the requirements of the schematic diagram, and check whether there are any cold solder joints on the solder joints on the circuit board. Or check whether the firmware has been burned to the chip, etc. First analyze whether it is caused by design problems or manufacturing process problems, and then report back to the supplier.
If you do not have the ability to check the problem, you can ask the supplier to send it back for inspection, or seek help from your design engineer to find the key problem and then report back to the supplier, and ask for improvement and discuss solutions to the problem.
Because the electronic manufacturing process is a complex process, any very small factor may cause product defects. When problems and disputes arise, you can discuss a win-win solution with the supplier.
We recommend that you make a few more spare parts each time you produce or proof-sample, and have the supplier keep at least one piece, or instruct the supplier to perform functional testing on the PCBA before shipment. This will greatly avoid the loss of time and money due to adverse reasons.